Table of Contents
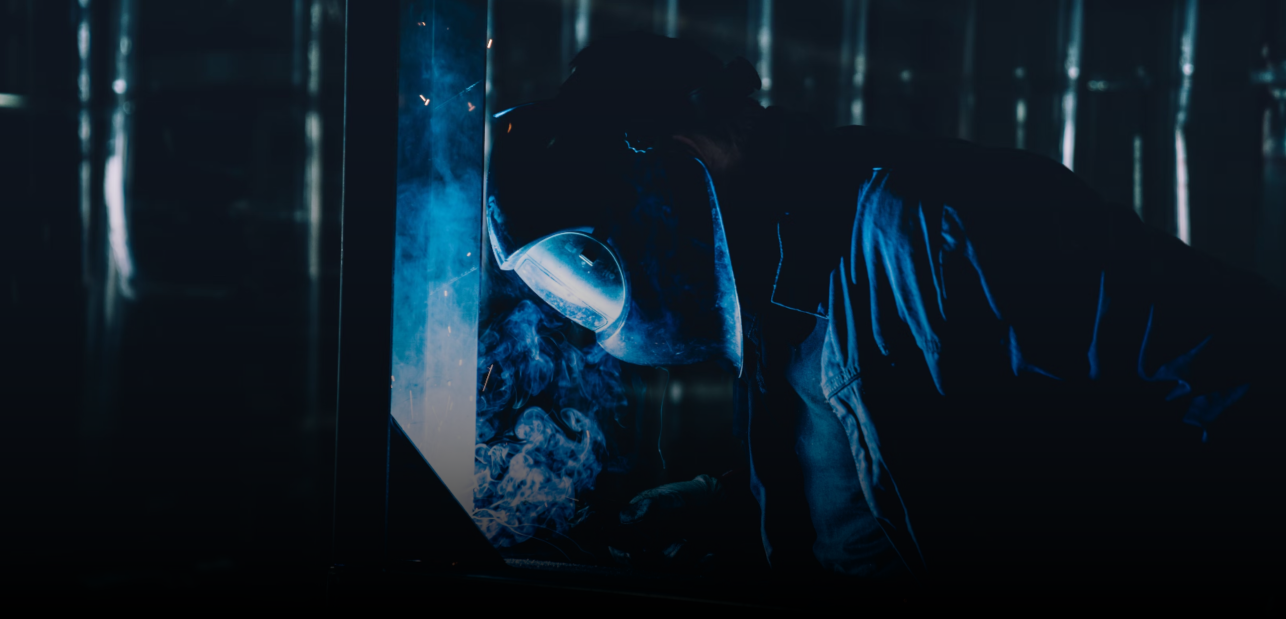
Aluminium is a lightweight, corrosion-resistant material used widely across automotive, marine, construction, and general fabrication sectors. Its appeal lies in its strength-to-weight ratio, but welding aluminium introduces challenges. Due to its thermal conductivity, oxide layer, and lower melting point, it behaves very differently from steel; for welders accustomed to mild steel, transitioning to aluminium demands both technique and the right tools.
Gas Metal Arc Welding (GMAW), commonly known as MIG welding, is a standard process for aluminium. This guide explores the basics of welding aluminium using MIG, covering key techniques and equipment. We also explore how the Strata AdvanceMig315C Compact MIG Package provides the reliability and performance needed for industrial aluminium applications.
Preparing Aluminium for MIG Welding
Before any arc is struck, aluminium must be thoroughly prepared. The surface of aluminium develops an oxide layer (aluminium oxide) that melts at a much higher temperature (around 2,072°C) than the base metal (660.3°C). This disparity in melting points can prevent proper fusion if the oxide is not removed.
The correct preparation process involves:
- Using a dedicated stainless-steel wire brush to remove oxide
- Avoiding steel brushes, which can contaminate the aluminium
- Cleaning the joint area with an approved degreaser (hydrocarbon-free)
- Repeating cleaning if there is any doubt
The presence of hydrocarbons (from cutting oils or fingerprints) and oxides can result in weld porosity and lack of fusion. As a rule, clean aluminium thoroughly, even if it appears ready for welding.
Failure to prepare the material properly in critical fabrication environments, such as aerospace or structural aluminium work, can lead to early weld failure. Adhering to industry-approved surface preparation standards enhances weld integrity and ensures compliance with quality assurance protocols demanded by clients and regulators.
Preheating for Improved Weld Quality
Aluminium has high thermal conductivity rapidly draws heat away from the weld zone. This makes starting the weld puddle more difficult and increases the chance of defects.
Preheating can help compensate for thicker materials or joints of dissimilar thickness. A moderate preheat, not exceeding 110°C, helps slow the heat dissipation and reduces the risk of cracking.
Use an infrared thermometer or temperature stick to monitor heat, and remember that overheating can degrade the material properties. Preheating is a standard practice when working with plates thicker than 6mm in many fabrication environments.
Preheating also contributes to improved productivity in high-volume workshop settings. It helps stabilise arc starts, reduces time spent reworking cracked joints, and enables greater penetration control on demanding weld paths. Additionally, evenly applied preheat supports consistent weld appearance across long seams or batch jobs, reinforcing the professional quality of the final product.
Selecting the Right Aluminium MIG Wire
Aluminium welding requires specific filler wires to match the alloy composition and service conditions. The two most common aluminium MIG wires are:
- ER4043: Aluminium-silicon alloy. Lower melting point, better wetting, and less crack sensitivity.
- ER5356: Aluminium-magnesium alloy. Stronger welds, suitable for anodising.
ER4043 is often used for casting and 6XXX series alloys. ER5356, in contrast, offers better ductility and strength, particularly with 5XXX series alloys. The choice depends on the base metal, weld strength requirements, and whether post-weld treatments are needed.
Wire diameter is another key factor. Thinner wire (0.8mm) is easier to control on light-gauge aluminium, while 1.0mm or 1.2mm is better for heavier work.
Smooth wire feed is critical. Aluminium wire is soft and prone to deformation. U-groove drive rollers help avoid wire shaving. Combined with a reliable feeding system, these ensure a steady arc and reduce downtime.
Choosing the correct wire and machine feed system combination directly impacts weld quality. An inconsistent feed can lead to arc instability, porosity, or undercutting. Modern wire feeders, especially with machines like the Strata AdvanceMig315C, help eliminate such issues through consistent torque and precision drive control.
Professionals often overlook the importance of correct wire tension and liner selection. A Teflon liner reduces friction and enhances feed consistency when welding aluminium. By optimising the entire feed path, from spool hub tension to contact tip fitment, welders can avoid issues like bird-nesting and achieve greater weld continuity.
Shielding Gas: Choosing the Right Type
Shielding gas protects the weld puddle from contamination. For aluminium MIG welding, the go-to shielding gas is 100% argon. It offers excellent arc stability, good cleaning action, and adequate penetration for most applications.
However, for thicker material (e.g. 10mm+), a mixture of 75% helium and 25% argon is sometimes used. Helium increases the arc temperature, improving penetration.
Gas flow should typically be 15–20 L/min. Too much flow can create turbulence, while too little risks oxidation. Always check the torch nozzle and regulator settings to maintain consistency.
Gas purity should not be neglected. Welders should aim for industrial-grade argon (99.99%) and ensure that hoses and fittings are leak-free. Contaminants introduced through the shielding gas line can undo even the most meticulous metal preparation.
Welding Technique: Settings and Motion
Due to its thermal conductivity, aluminium requires higher voltage and amperage than steel. The arc should operate in spray transfer mode, providing a smooth, stable arc with minimal spatter.
Key technique points:
- Use a push angle, not drag, for better shielding and cleaning
- Maintain a consistent torch distance (10–15mm)
- Keep travel speed high to avoid overheating
- Minimise dwell time to prevent burn-through on thin material
Avoid weaving unless necessary. A straight pass is generally more effective with aluminium. Weld bead shape should be slightly convex, not flat or concave, to reduce the risk of cracking. Additionally, consistent torch motion is vital. Erratic movement can result in uneven heat input, leading to undercutting or erratic bead appearance.
Crater Cracking: How to Prevent It
One of the common issues in aluminium welding is crater cracking. This occurs at the end of a weld when the crater cools and contracts rapidly. A concave crater shape concentrates the contraction force, leading to cracks.
To avoid this:
- Fill the weld crater before stopping
- Aim for a convex crater shape
- Use crater fill or 4T mode on compatible machines
The convex shape compensates for shrinkage, reducing stress on the weld endpoint. Manual techniques, like a short backfill before stopping, also help.
Operators should be trained to monitor crater formation in real time and not rely solely on automatic settings. Though subtle, this attention to weld termination directly affects long-term structural integrity.
The Strata AdvanceMig315C: Tailored for Aluminium MIG
For professionals seeking high-performance aluminium welding capabilities, the Strata AdvanceMig315C 315A Compact MIG Package stands out as a purpose-built solution engineered for demanding industrial applications. Combining precision control, rugged construction, and advanced arc technology, this machine is ideal for aluminium fabricators, trailer manufacturers, marine engineers, and anyone working with softer non-ferrous metals.
Why It Excels at Aluminium Welding:
- IGBT Inverter Technology: This technology delivers a stable and responsive arc with maximum efficiency, which is critical for controlling heat input and minimising distortion on thin aluminium sections.
- 4-Roll Geared Wire Feed System: Soft aluminium wire requires smooth and steady feeding to prevent burn-back and bird-nesting. The robust metal 4-roll system ensures reliable delivery, even with wire with a diameter of 0.6–1.0mm.
- Spool Gun Compatibility: This kit includes a remote spool gun connection, which gives you the option of a short wire path for softer wires like aluminium. This dramatically reduces feeding issues and improves arc starts.
- Digital Microprocessor Control: Welders gain fine-tuned command over arc characteristics, voltage, and wire speed. This is ideal for those needing precise control when switching between alloys or material thicknesses.
- Advanced Welding Modes: This feature includes adjustable pre-flow, post-flow, burn-back, and soft start—critical when dialling in the perfect settings for aluminium, especially during out-of-position or extended welds.
- Crater Fill & 2T/4T Trigger Control: These functions help create smoother arc terminations and consistent bead profiles on long aluminium runs, eliminating weak stop points or excessive crater cracks.
- Industrial Protection & Durability: With an IP23 casing and integrated over-temperature, over-voltage, and surge protection, the AdvanceMig315C is built for tough New Zealand workshop environments. It’s even stress-tested up to 550V and compatible with generator power, so you can take it on-site with confidence.
Practical Summary for Workshop Use
- Material Prep: Remove oxide with stainless brush, degrease surfaces
- Wire Selection: Choose ER4043 or ER5356 based on the base alloy
- Shielding gas: Use 100% argon for most jobs, argon-helium mix for thick plate
- Technique: Push angle, consistent speed, no weaving
- Crater Control: Build up weld craters to avoid cracking
- Preheat: Use when needed, especially for heavy or mixed sections
- Equipment: Use reliable MIG welders like the Strata AdvanceMig315C for consistent results
Aluminium presents unique welding challenges that demand precision, preparation, and quality equipment. MIG welding efficiently joins aluminium, provided the correct parameters and techniques are followed.
Those looking to improve aluminium welding results should consider adopting the abovementioned practices. When you're ready to upgrade your equipment, the Strata AdvanceMig315C 315A Compact MIG Package from Proline Industrial is prepared to meet the task. Explore the full range of MIG welders and accessories at Proline Industrial. For personalised recommendations or expert advice, reach out to our team – we're here to help you weld with precision and confidence.