Table of Contents
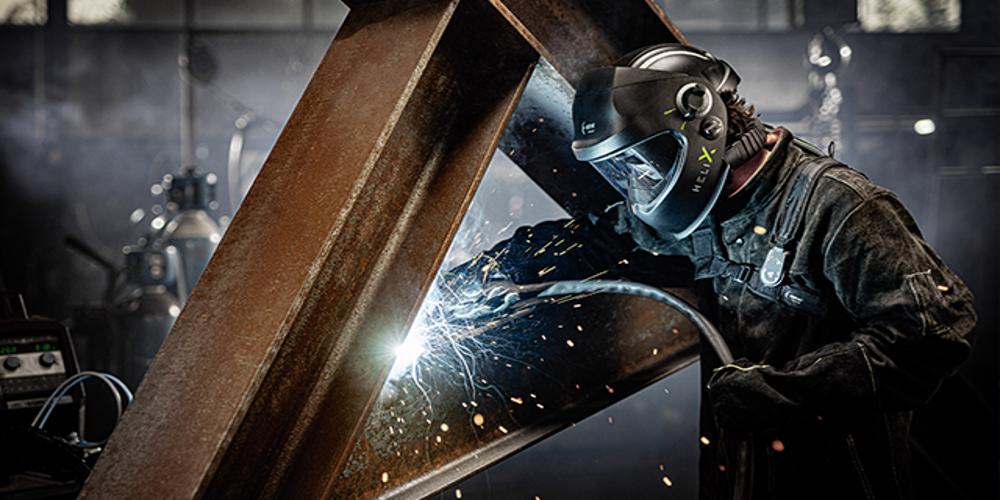
Welding is at the heart of many industries across New Zealand—from heavy construction and engineering to agricultural repairs and precision fabrication. Still, while much attention is given to weld quality and structural strength, welding fumes are a less visible danger that deserves equal focus.
These fumes aren’t just irritants but a serious health hazard. In 2018, the International Agency for Research on Cancer (IARC) officially classified welding fume as “carcinogenic to humans”, placing it in Group 1, the same category as asbestos and tobacco smoke. This classification confirms what health experts have long suspected: long-term exposure to welding fumes can cause cancer.
This revelation is a call to action for welders, workshop supervisors, and business owners. Protecting your team isn’t just about ticking compliance boxes—it’s about making sure skilled professionals have the equipment they need to stay safe on the job.
In this article, we’ll explain welding fumes, the health symptoms they can cause, and the protective solutions available to reduce exposure so you can make informed decisions about workplace safety and respiratory protection.
Understanding the Risk: What Are Welding Fumes?
Welding fume is a complex mix of fine metal particles and gases released when metals are heated above 4000°C. These fumes originate from the consumables used—electrodes, wires, rods—and the base metals. Depending on the type of welding, the emissions can include:
- Hexavalent chromium (from stainless steel)
- Cadmium and zinc oxide (from galvanised steel)
- Nickel, manganese, and iron oxide
- Gases like ozone, carbon monoxide, and nitrogen oxides
Inhaling these substances, even in small amounts, can lead to:
- Short-term illnesses like metal fume fever
- Respiratory irritation and lung inflammation
- Long-term diseases, including lung cancer and kidney cancer
For example, cadmium in some welding materials is highly toxic and leads to flu-like symptoms when inhaled, known as metal fume fever. Inhaling hexavalent chromium poses a direct cancer risk and is also mutagenic. Prolonged exposure to manganese has been associated with neurological effects similar to Parkinson's disease.
WorkSafe NZ and Evolving Standards
Traditionally, exposure to welding fumes in New Zealand was measured using a general Workplace Exposure Standard (WES) of 5 mg/m³ as an 8-hour time-weighted average. However, WorkSafe has acknowledged that this broad standard no longer reflects the diverse toxicity of welding fume components.
Today, safety regulators emphasise reviewing each hazardous metal separately. For instance:
- Hexavalent chromium: WES-TWA is significantly below 5 mg/m³.
- Cadmium and nickel have lower permissible exposure limits.
Rather than relying on a single number, the modern approach requires employers to:
- Identify the specific metals in welding electrodes and base materials (via Safety Data Sheets).
- Measure air quality in work zones using personal air sampling techniques.
- Compare airborne exposure results with specific WES values.
- Implement control measures if readings exceed safe limits.
This method ensures that each worker is protected from general particulates and specific substances known to cause harm.
Why Health Monitoring Matters
Even when visible fumes are controlled, microscopic particles still pose health risks. That's why biological monitoring is now a recommended practice.
Common tests include:
- Urinary chromium analysis for welders using stainless steel
- Cadmium and fluoride checks for those working with treated steels
- Spirometry to assess lung function over time
Research also indicates that female welders may carry higher burdens of metal exposure, which raises special concerns regarding reproductive health and long-term toxicity.
The use of structured respiratory health questionnaires should accompany health monitoring. These help identify early symptoms such as:
- Persistent coughing
- Shortness of breath
- Wheezing or fatigue during physical tasks
Workshops can combine biological sampling with these evaluations to detect early signs of occupational illness, enabling proactive intervention.
Controlling Exposure with Engineering and PPE
The hierarchy of control starts with elimination, but that's rarely possible in welding. The next best practice is substitution—choosing materials with lower emission profiles. However, due to job requirements, most New Zealand fabricators continue to work with various metals and coatings.
This makes engineering controls and personal protective equipment (PPE) crucial. Key controls include:
1. Local Exhaust Ventilation (LEV)
LEV systems are positioned close to the welding arc and remove fumes before they can spread into the worker’s breathing zone. These systems are among the most effective ways to manage exposure, capturing harmful particulates at the source. Common solutions include:
- Flexible extractor arms mounted to benches or walls
- Welding tables with integrated downdraft extraction
- Portable fume extractors that can move between workstations
A standout example of portable LEV is the Strata AirForce M20 Twin-Motor Fume Extractor—a compact yet powerful unit built specifically for professional welding environments. What sets the M20 apart is its intelligent pairing with the XM Torch 2M, which allows direct fume extraction right from the welding torch, capturing contaminants before they disperse.
This system uses two heavy-duty Bypass motors, each delivering up to 190 m³/h airflow and offering exceptional suction performance. Depending on the job, operators can manage each motor individually for full control over intake strength. A sensitive current sensor attached to the welding machine’s ground cable automatically activates the extractor when welding begins, synchronising operation and reducing the risk of oversight.
Key Features of the Strata AirForce M20:
- 2600W total power output from dual motors
- 20L tank capacity and 3.5m² filter surface area
- M Class certified polyester filter traps particles as small as 1 micron
- Optional H14 filter available for maximum protection
- JetClean® filter cleaning system maintains airflow during extended use
- Quiet operation thanks to an insulated motor housing
- Auto start/stop function via the sensor clip on the welding ground cable
- Suction inlet: 40mm diameter
- Compact footprint - 534 x 471 x 983mm, weighing 38kg
Designed for industrial environments where space, mobility, and air quality matter, the AirForce M20 is a smart investment for workshops looking to control welding fumes at the source—especially those working with stainless, galvanised, or painted materials.
2. General Workshop Ventilation
While not replacing local extraction, general ventilation is essential in maintaining safe air quality. It works by diluting residual fumes that aren’t captured at the source and helps promote a healthier, more breathable environment throughout the workshop.
In addition to open doors, roof vents, and fixed mechanical systems, portable air movement solutions are beneficial, especially in temporary work areas or awkward spaces like containers, pits, or confined bays.
A practical example is the Portable Air Extraction and Ventilation Fan, a rugged and mobile unit designed to extract contaminated air or supply clean, cool air into a work zone. By increasing air circulation, this unit can significantly improve thermal comfort and fume dispersion, leading to safer and more productive working conditions for welders.
These fans are available in two diameters—300mm and 450mm—each built with a heavy-duty steel case, safety grills, carry handles, and rubber-mounted feet for vibration reduction and stability. They're ideal for workshops, on-site welding, and maintenance environments.
Key Features:
300mm Model:
- Airflow: 60m³/min
- Pressure: 370 Pa
- Power: 520W motor
- Compact and easy to transport
- Optional 5m or 10m ducting kits available for targeted airflow
450mm Model:
- Airflow: 125m³/min
- Pressure: 972 Pa
- High-performance output for larger spaces
- Also compatible with 5m or 10m ducting kits
Whether used to pull hot, contaminated air out or to push fresh air into a space, these units offer a low-cost, high-impact solution to enhance air quality, especially in workshops where fixed ventilation systems are insufficient or unavailable.
3. Safe Work Practices
- Avoid welding painted, oiled, or chemically treated surfaces without pre-cleaning.
- Position yourself to avoid the fume plume—"keep your head out of the smoke."
- Use grinders and plasma cutters in well-ventilated or extraction-supported areas.
4. Personal Protective Equipment (PPE)
Respiratory protection is often the final line of defence. Traditional P2 or half-mask respirators filter out particles, but come with limitations:
- Require a tight face seal
- Create breathing resistance
- Can fog up visors during long tasks
- Uncomfortable for long shifts
This is where advanced systems like Powered Air-Purifying Respirators (PAPRs) come into play.
The Optrel Swiss Air PAPR & Clearmaxx Helmet Kit
The Optrel Swiss Air PAPR Multi-Use Respiratory System, combined with the Clearmaxx Grinding Helmet, delivers a premium solution for respiratory protection and visual clarity for welders working in confined, dusty, or high-fume environments. This system goes beyond traditional PPE—it redefines comfort, independence, and safety for those working in harsh conditions.
What Makes the Optrel Swiss Air Different?
At the heart of the Swiss Air system is a flame-retardant, ventilated half-mask made from high-tech fabric. It covers the mouth and nose completely, delivering purified, filtered air directly to the breathing zone. By creating a positive pressure breathing space, the system significantly reduces fatigue and eliminates the resistance felt with conventional respirators. This makes it ideal for long shifts and high-output environments.
The TH3 filter unit—the highest level of filtration classification for PAPR systems—removes 99.8% of harmful particles, aerosols, vapours, smoke, and even viruses. Whether you’re exposed to galvanised steel fumes, silica dust, organic particulates, or chemical vapours, the Swiss Air has you covered.
Key Features:
- TH3-certified filtration removes 99.8% of all harmful airborne substances
- Positive pressure airflow supports breathing, minimises fatigue
- Adjustable airflow control to prevent dry eyes or fogging
- Automatic airflow calibration for consistent protection regardless of altitude or temperature
- Integrated control panel shows battery level, airflow settings, and system diagnostics
- 14-hour battery life keeps you protected all day
- Freely adjustable head harness fits head sizes XS–XL comfortably
- No face-fit test required—perfect for users with facial hair or sensitive skin
- Ergonomic and lightweight blower unit for all-day wear
- Compatible with any welding helmet—can be worn independently or under other PPE
Real-World Applications
Optrel Swiss Air kit meets the needs of professionals across many trades:
- Welders handling stainless, galvanised, or heavy-duty materials
- Engineers needing high mobility and respiratory protection
- Concrete workers dealing with silica and cement dust
- Joiners and cabinetmakers are exposed to wood dust
- Agricultural workers handling fertilisers, seed dust, or organic compounds
- Painting, sandblasting and industrial cleaning crews
Click below to see the Swiss Air in Action:
Creating a Culture of Respiratory Safety
The most effective safety programmes go beyond equipment. They are built on a foundation of:
- Training workers on the risks of welding fumes
- Maintaining fume extraction systems and air monitors
- Encouraging proper use of PPE without shortcuts
- Including health and safety in daily routines
Workshops should normalise talking about lung health, encourage flu and pneumococcal vaccinations, and ensure that both apprentices and senior tradespeople are engaged in safety decisions.
When welders see that management is investing in their health—whether through the purchase of Swiss Air systems or scheduled health monitoring—they are far more likely to adopt and maintain safe habits.
It's Time to Prioritise Clean Air in Welding
Welding fumes are no longer just a nuisance but a scientifically confirmed occupational hazard. The recognition of welding fumes as a Group 1 carcinogen demands more than lip service; it calls for action.
There are clear paths to reducing exposure, from understanding your consumables to implementing engineering controls and using best-in-class PPE like the Optrel Swiss Air PAPR system.
Workshops and businesses that invest in respiratory safety:
- Protect their workers' health
- Reduce absenteeism and health-related costs
- Stay compliant with evolving regulations
- Boost morale and productivity
Take control of your airspace today! Talk to the team at Proline Industrial about solutions tailored for your workshop. Whether it's air quality measurement, ventilation planning, or supplying the latest in PAPR technology, we're here to support your team's safety—one breath at a time.